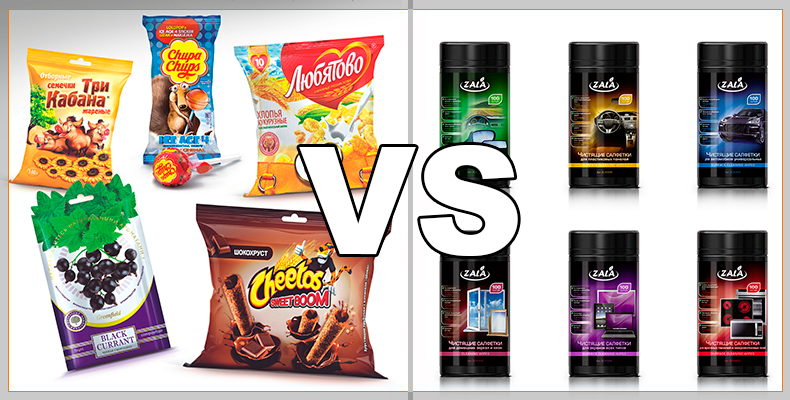
In today’s highly competitive market environment, packaging is no longer merely the “outer garment” of a product; it is a direct reflection of brand image and plays a critical role in product protection, transportation, and sales. Statistics show that approximately 70% of consumers are influenced by packaging when making purchasing decisions. An attractive package can quickly capture consumers’ attention amidst a sea of competing products, sparking their desire to buy.
However, businesses often face a dilemma when choosing packaging for their products: should they opt for flexible pouches, which offer unique advantages, or rigid packaging, known for its sturdiness and durability? This decision is not straightforward, as both options differ significantly in materials, performance, and cost, requiring a comprehensive evaluation of multiple factors.
1. Unveiling Flexible Pouches
1.1 Structure and Materials of Flexible Pouches
Flexible pouches, a common packaging form, are ubiquitous in the modern consumer goods market. They are typically made from multiple layers of composite films, each serving a distinct function, together forming the pouch’s structure.
Polyethylene (PE) is one of the most commonly used materials in pouch production. It boasts excellent flexibility, feeling soft to the touch, much like everyday plastic bags that can be easily folded or bent. This flexibility allows pouches to conform to products of various shapes, making them suitable for packaging irregularly shaped items. Additionally, polyethylene offers outstanding chemical corrosion resistance, effectively withstanding acids and alkalis (unless they are highly aggressive), ensuring stability when packaging products with chemical components.
Polypropylene (PP) is another prevalent pouch material. Compared to polyethylene, it is slightly harder and has a translucent, lightweight appearance. Polypropylene excels in heat resistance, maintaining shape stability at high temperatures without deforming easily. For instance, in food packaging requiring high-temperature sterilization, polypropylene pouches perform reliably, ensuring the packaging remains intact and preserves food quality.
Other materials are also commonly used in pouch production. Polyester (PET) films, for example, offer high strength and excellent barrier properties, effectively blocking oxygen and moisture to extend product shelf life. They are often used in food packaging with high preservation requirements, such as vacuum-packed deli meats. Nylon (PA), known for its superior abrasion resistance and puncture resistance, is ideal for packaging sharp or abrasive products, providing enhanced protection against damage. These different films are combined through lamination techniques, leveraging their respective strengths to endow pouches with diverse performance capabilities.
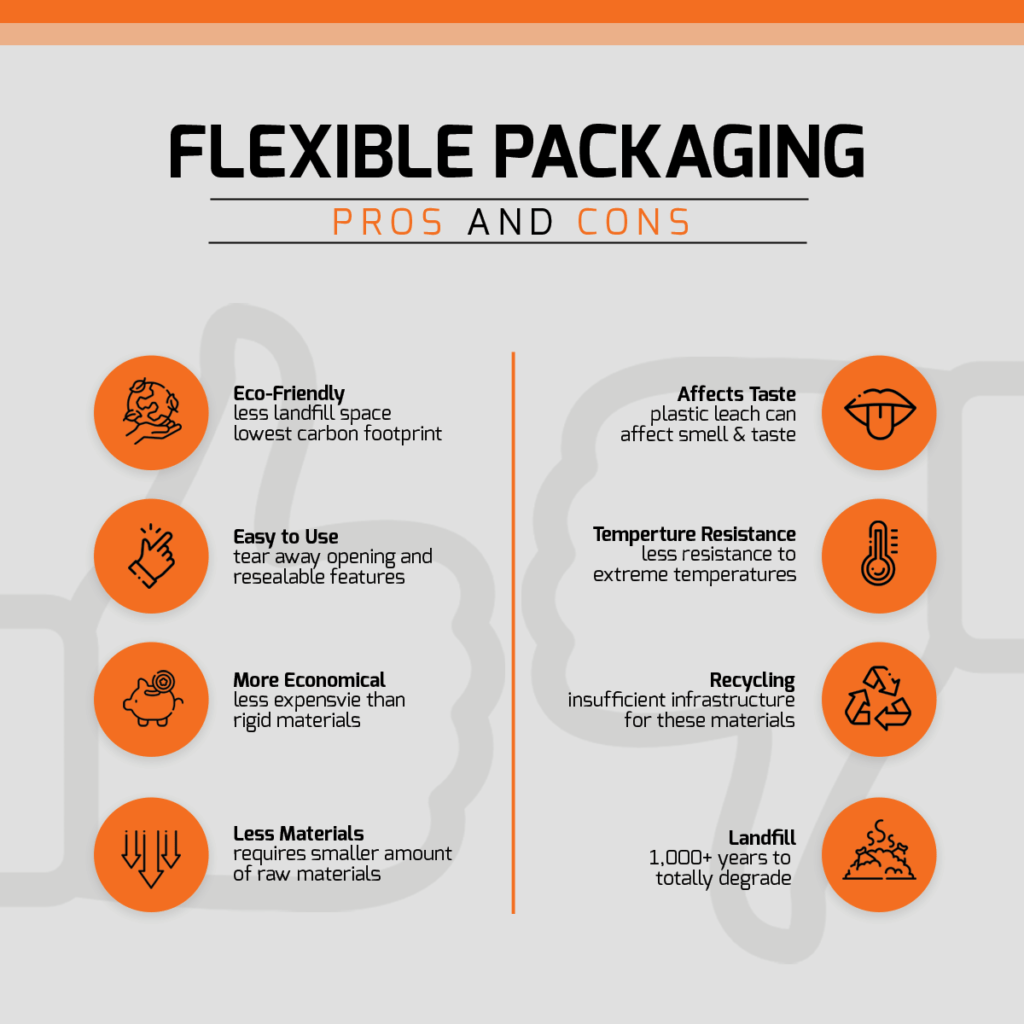
1.2 Advantages of Flexible Pouches
Significant Cost Efficiency: Cost is a critical factor in the packaging industry, and flexible pouches excel in cost control. The materials used, such as plastic films and thin paper layers, are far less expensive than rigid materials like glass, metal, or thick cardboard. For example, the material cost for an average plastic pouch may be just a few cents, whereas a glass container of the same size and purpose could cost several dollars. In large-scale production, this cost difference translates into substantial savings for businesses. Moreover, the relatively simple structure of pouches streamlines production processes, boosting efficiency and further reducing costs. Data suggests that products packaged in pouches can reduce packaging costs by 20% to 50% compared to rigid packaging.
Efficient Space Utilization: The flexibility of pouches provides unique advantages in space utilization. During transportation and storage, pouches can be easily folded or compressed, occupying minimal space. Imagine comparing a stack of soft snack pouches to the same number of rigid plastic bottles: pouches can be tightly stacked, while rigid bottles, due to their fixed shapes, leave gaps, wasting space. Tests show that, for the same product volume, pouch packaging can increase loading capacity in transport vehicles or warehouses by 30% to 50%, significantly reducing transportation and storage costs and improving logistics efficiency.
Flexible and Diverse Design: Packaging design is a key tool for attracting consumers, and pouches offer businesses vast creative freedom. Their surfaces support advanced printing technologies, such as digital or gravure printing, enabling high-quality graphics, logos, product information, and promotional content. These vibrant, detailed prints clearly showcase product features and brand identity, helping products stand out on shelves. For instance, some cosmetic brands use pouches with exquisite printing to highlight product benefits, ingredients, and stylish designs, captivating consumers. Additionally, pouches can be shaped into various forms—square, round, irregular, or with unique features—to meet diverse product packaging needs.
Strong Environmental Attributes: With growing global emphasis on environmental protection, the eco-friendliness of packaging has become a key consideration. Pouches offer clear advantages in this regard. They typically use fewer materials, reducing resource consumption during production compared to heavier rigid packaging, thus alleviating pressure on natural resources. Many pouch materials, such as polyethylene and polypropylene, are recyclable, allowing them to be repurposed after processing, reducing landfill waste and environmental pollution. Some pouches also incorporate biodegradable materials that decompose naturally, avoiding the long-term environmental harm caused by traditional plastics and contributing to sustainable development.
Versatile and Practical Functionality: Beyond appearance and cost, pouches excel in functionality. Through thoughtful material selection and structural design, they can offer excellent barrier properties, effectively shielding products from moisture, oxygen, light, and contaminants. In the food industry, pouches prevent spoilage and oxidation, extending shelf life and reducing waste. In pharmaceuticals, they protect drugs from environmental interference, ensuring quality and efficacy. Some pouches also feature specialized functions, such as anti-static or UV-resistant properties, meeting the unique packaging needs of various products and providing comprehensive protection.
1.3 Limitations of Flexible Pouches
Limited Protection: Despite their many strengths, pouches have limitations in product protection. Compared to rigid packaging, their softer texture offers weaker cushioning against external impacts. For example, if a pouch containing a product is dropped or squeezed, the contents are more likely to be damaged. For fragile items like glass products or precision electronics, pouches provide insufficient protection, with a higher risk of breakage. Tests indicate that, under identical transport and storage conditions, fragile products in pouches have a 15% to 30% higher damage rate than those in rigid packaging.
Perception of Lower Quality: In consumers’ minds, packaging texture often correlates with product quality and prestige. Due to their material and appearance, pouches may feel relatively inexpensive, potentially undermining the brand image of premium products. High-end consumers often prefer rigid packaging, which conveys sturdiness, durability, and sophistication. For instance, luxury cosmetics or jewelry rarely use pouches, opting instead for elegant, high-quality rigid boxes to enhance perceived quality and brand image.
Limited Barrier Performance: While pouches can enhance barrier properties through material lamination, their performance may fall short in extreme conditions compared to some rigid packaging. In high-humidity or high-temperature environments, pouches may experience reduced resistance to moisture and oxygen, shortening product shelf life. For products with stringent storage requirements, such as certain high-end foods or pharmaceuticals, pouches may not meet long-term preservation needs. Additionally, pouches are less effective at blocking odors, which can be problematic for products prone to absorbing external smells.
2. In-Depth Analysis of Rigid Packaging
2.1 Composition and Materials of Rigid Packaging
Rigid packaging, as the name suggests, is made from high-hardness, high-strength materials that provide robust and durable protection for products in various environments.
Glass, a long-standing and widely used rigid packaging material, offers high transparency, allowing consumers to clearly see a product’s appearance, color, and texture. This is particularly appealing for products like premium alcoholic beverages or cosmetics, where visual presentation is key. Glass also boasts excellent chemical stability, rarely reacting with most substances, making it ideal for preserving chemically sensitive products like pharmaceuticals or food additives. However, glass is brittle and prone to breaking, requiring extra care during transportation and use.
Metal, including tinplate and aluminum, is another common rigid packaging material. Tinplate offers strong mechanical strength and excellent barrier properties, effectively blocking oxygen, moisture, and light, making it ideal for canned foods or powdered milk containers. Aluminum, lightweight and highly corrosion-resistant, is easily processed into various shapes, such as beverage cans or pharmaceutical foil packaging. However, metal materials are relatively costly and require significant energy during production.
Rigid plastics, such as polyethylene terephthalate (PET) and high-density polyethylene (HDPE), play a major role in rigid packaging. PET offers high transparency, strength, and toughness, along with good barrier properties, making it widely used for beverage bottles, cooking oil containers, and cosmetic bottles. HDPE is valued for its excellent chemical resistance and rigidity, commonly used for detergent or pesticide bottles. Rigid plastics are relatively low-cost and benefit from mature production processes, enabling large-scale manufacturing. However, some rigid plastics are less environmentally friendly, as they are difficult to degrade naturally, posing environmental challenges.
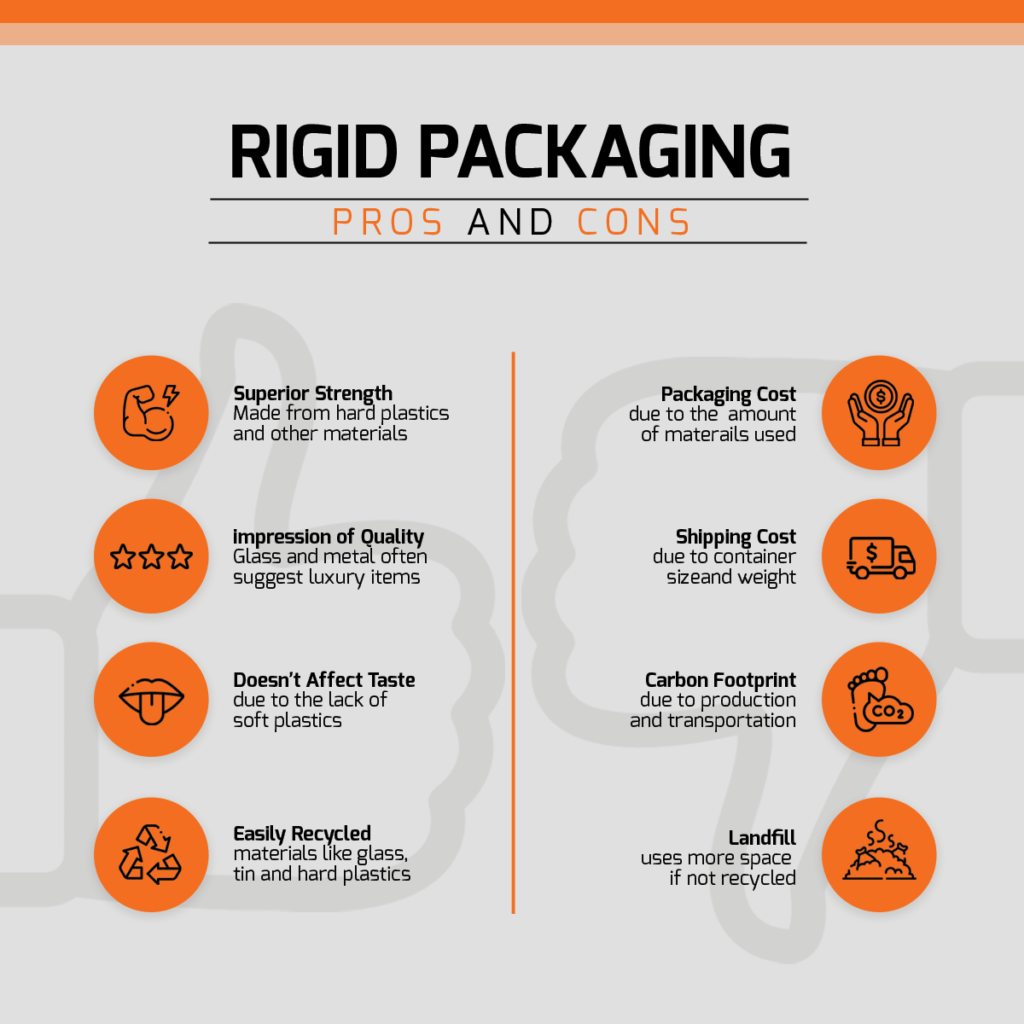
3. Packaging Choices Based on Product Characteristics
3.1 Food and Beverage Industry
In the food and beverage sector, both flexible pouches and rigid packaging have distinct applications. For liquid beverages like milk, juice, or drinking water, flexible pouches are favored for their portability, ease of use, and lower cost. Tetra Pak milk cartons, for example, use multilayer composite pouches that effectively block oxygen and light, extending shelf life while being convenient for consumers to carry and store. Pouches also save space and reduce transportation costs.
For snack foods like chips, nuts, or candies, flexible pouches excel. Their ability to feature vibrant, eye-catching designs enhances product appeal, while their flexibility accommodates various snack shapes and provides adequate protection. Inflated pouches for chips, for instance, prevent breakage during transportation and maintain crispness.
However, for premium alcoholic beverages like wine or whiskey, rigid packaging better reflects quality and prestige. Glass wine bottles offer high transparency, showcasing the liquor’s color and clarity, and their chemical stability ensures quality and flavor preservation. Some premium wine bottles incorporate unique designs, such as engravings or frosted finishes, to further elevate brand image and value.
Canned foods typically use metal or glass rigid packaging. Metal cans provide excellent sealing and corrosion resistance, protecting food from environmental factors and extending shelf life. Glass jars allow consumers to see the contents, building trust, and are commonly used for fruit or meat preserves.
3.2 Personal Care and Cosmetics
In the personal care and cosmetics industry, packaging choices depend on product characteristics. For lotions or creams, which are viscous and require controlled dispensing, rigid packaging like plastic bottles or tubes is common. Plastic bottles offer reliable sealing and stability, preventing leaks or spoilage, while tubes allow easy squeezing and customizable nozzle designs to meet consumer preferences.
Lipsticks or eyebrow pencils typically use metal or plastic rigid packaging. These protect the product’s shape and texture while offering elegant designs that enhance fashion appeal. High-end lipstick brands often use metal casings with intricate engravings, blending utility with artistry.
For perfumes, glass bottles are the standard. Glass’s transparency and luster showcase the perfume’s color and texture, while its barrier properties prevent evaporation or degradation. Perfume bottle designs emphasize artistry and uniqueness, with iconic examples like Chanel No. 5’s minimalist square bottle becoming a hallmark of elegance.
However, flexible pouches are widely used for cosmetic samples or trial packs. Their low cost and compact size make them ideal for portability and distribution, allowing consumers to test products like face masks conveniently.
3.3 Pharmaceuticals and Healthcare Products
Pharmaceutical and healthcare products have stringent packaging requirements to ensure quality, safety, and regulatory compliance. For solid medications like tablets or capsules, blister packs—a form of flexible packaging—are common. Made by heat-sealing plastic films with aluminum foil, blister packs effectively block oxygen and moisture, preserving drug quality. They also enable single-dose packaging, improving patient convenience and reducing waste.
For liquid medications like oral solutions or syrups, plastic or glass bottles are typical rigid packaging choices. Plastic bottles are lightweight and shatter-resistant, ideal for children’s medications or portable drugs. Glass bottles offer superior chemical stability and barrier properties, suitable for medications with strict storage requirements.
Healthcare products follow similar patterns. For long-term storage of sensitive items like vitamins or fish oil, rigid packaging provides better protection. For portable healthcare products like probiotic sachets or energy bars, flexible pouches are more convenient for carrying and consumption.
4. Cost Considerations: Short-Term vs. Long-Term Trade-Offs
4.1 Initial Procurement Cost Comparison
Flexible pouches generally have a clear advantage in initial procurement costs. Their primary materials, such as plastic films or thin paper layers, are relatively inexpensive, and their simple production processes require less complex molds or high-precision equipment, significantly lowering manufacturing costs. For example, a typical snack pouch may cost just a few cents per unit.
In contrast, rigid packaging has higher initial procurement costs. Materials like glass and metal are costly, particularly for specialized or high-quality variants. The production process is more complex, involving high-temperature firing for glass or stamping and welding for metal, which increases costs. A standard glass beverage bottle may cost several times more than a pouch of equivalent capacity, and even lower-cost rigid plastics typically exceed pouch costs.
Packaging size and customization also impact costs. Flexible pouches offer greater flexibility in size and shape, keeping cost increases minimal for small-batch or customized orders. Rigid packaging, due to high mold costs, sees significant unit cost increases for small or specialized orders.
4.2 Long-Term Usage Cost Analysis
In terms of long-term usage costs, both flexible pouches and rigid packaging have distinct characteristics. For transportation, pouches’ lightweight and foldable nature saves significant space and weight, reducing costs. Data shows that products in pouches can lower transportation costs by 10% to 30% compared to rigid packaging. For instance, during long-distance shipping, pouches can be tightly stacked, reducing vehicle space usage and fuel consumption.
In warehousing, pouches also shine. They can be folded and stacked, occupying less space and requiring no special storage equipment or conditions. Rigid packaging, with its fixed shapes, demands more storage space, and fragile rigid packaging may require additional protective measures, increasing costs.
However, rigid packaging excels in reducing product loss. Its superior protective properties minimize damage during transportation and storage, particularly for fragile or easily damaged products like glassware or electronics, lowering long-term costs by reducing losses.
Recycling costs present challenges for both. While some pouch materials are recyclable, their complex structures and compositions increase recycling difficulty and costs. Multilayer composite pouches require intricate separation processes. Glass and metal in rigid packaging are recyclable but involve energy-intensive processes and high technical costs. Rigid plastics, particularly non-degradable types, pose significant recycling challenges, contributing to long-term environmental and societal costs.
5. Environmental Perspective: The Need for Sustainability
5.1 Recyclability of Packaging Materials
With global emphasis on environmental protection and sustainability, the recyclability of packaging materials is a critical factor. Both flexible pouches and rigid packaging have unique characteristics, challenges, and opportunities in this regard.
Flexible pouches often have complex material compositions, typically involving multiple laminated plastic films, which complicates recycling. Polyethylene (PE) and polypropylene (PP), common pouch materials, are theoretically recyclable. However, in practice, printing inks, adhesives, and other additives can degrade recycled plastic quality, limiting its use to lower-grade products. For example, snack pouches, while made from recyclable plastics, require complex processes to remove inks and adhesives, and their lightweight, thin nature can jam recycling equipment, raising costs. Pouches with aluminum foil or metal-plastic composites further increase recycling complexity, requiring specialized separation technologies.
In contrast, some rigid packaging materials offer recycling advantages. Glass is highly recyclable, capable of infinite reuse without loss of physical properties. Many cities have established glass recycling systems, allowing discarded bottles to be cleaned, melted, and reshaped into new containers. Metal packaging, such as tinplate and aluminum, also has high recycling value. Recycling aluminum cans saves approximately 95% of the energy required to produce new cans, reducing resource extraction and energy use.
However, rigid plastic recycling is less promising. Materials like PET and HDPE are recyclable in theory, but practical challenges abound. Consumers often struggle to sort different plastics accurately, leading to mixed recycling streams that degrade quality. Recycling technologies and infrastructure for rigid plastics are also underdeveloped, and high costs reduce recycling incentives for businesses.
5.2 Environmental Impact of Production Processes
The environmental impact of packaging production is another key factor, with flexible pouches and rigid packaging differing significantly in energy consumption and pollutant emissions.
Flexible pouch production is relatively simple, involving processes like film extrusion, lamination, and printing. Energy consumption is low, as production equipment operates at lower power levels, and the lightweight, thin materials reduce energy use in raw material processing and transportation. The main pollutants are volatile organic compounds (VOCs) from printing inks and adhesives. Some manufacturers use eco-friendly inks and adhesives, along with efficient waste gas treatment systems like activated carbon adsorption or catalytic combustion, to reduce VOC emissions.
Rigid packaging production is more complex and energy-intensive. Glass production requires high-temperature firing (around 1500°C) to melt raw materials like quartz sand, soda ash, and limestone, consuming significant fossil fuels like coal or natural gas and emitting substantial carbon dioxide. Metal packaging production also demands high energy for mining, smelting, and processing, generating waste slag, wastewater, and emissions. Metal smelting can produce heavy metal-containing wastewater, which, if untreated, pollutes soil and water. Rigid plastic production consumes less energy than glass or metal but still generates pollutants like plastic dust and waste gases, which can harm the environment and health if not managed properly.
5.3 Consumer Environmental Awareness and Choices
As environmental awareness grows, consumers are increasingly influenced by packaging sustainability when making purchasing decisions. Surveys show that about 70% of consumers prefer products with eco-friendly packaging when other factors are equal. This shift in preferences is pushing businesses to prioritize sustainable packaging solutions.
Consumers favor recyclable and biodegradable packaging, hoping their purchases minimize long-term environmental harm. Health-conscious and eco-minded consumers also scrutinize packaging for safety, ensuring no harmful substances migrate into products. Products with eco-friendly packaging, such as biodegradable plastic pouches for food, have gained market traction, with rising sales as consumers see these choices as contributions to environmental protection.
This growing consumer awareness is driving businesses to invest in sustainable packaging research and adoption. Companies are introducing recyclable materials, minimalist designs, and reduced packaging layers to meet consumer demands. Some also engage in consumer education to raise awareness and acceptance of eco-friendly packaging, further aligning with market trends.
6. Future Trends Outlook
6.1 Innovations in Packaging Technology
As technology advances rapidly, both flexible pouches and rigid packaging are undergoing innovative transformations to meet increasingly diverse and stringent market demands.
In flexible pouch technology, new material development is a key focus. Significant progress has been made in biodegradable materials, with research institutions and businesses developing alternatives to non-degradable plastic films. Bio-based materials like polylactic acid (PLA) and polyhydroxyalkanoates (PHA) are increasingly used in pouches. These materials offer good biodegradability, breaking down naturally to reduce environmental pollution, while maintaining essential properties like flexibility, strength, and barrier performance.
Smart flexible pouches are another emerging trend. By integrating sensors or electronic tags, pouches can monitor product conditions in real time and transmit data. For example, some food pouches incorporate time-temperature indicators to track storage conditions, allowing consumers to assess freshness. Others use radio-frequency identification (RFID) technology to enhance supply chain tracking and management efficiency.
In rigid packaging, new material development is equally critical. High-strength, lightweight materials are being explored to reduce packaging weight, lower transportation costs, and improve durability. Novel aluminum alloys, for instance, reduce metal packaging weight while enhancing corrosion resistance and processability. In plastics, modified engineering plastics offer improved rigidity, barrier properties, and heat resistance.
Smart rigid packaging is also advancing. Smart bottle caps with sensors can monitor opening frequency or remaining contents, transmitting data to consumers’ smartphones via Bluetooth for a more convenient experience. Some pharmaceutical rigid packaging incorporates tamper-proof or child-resistant designs, using specialized structures and materials to enhance safety and prevent misuse.
6.2 Predictions for Changing Market Demand
Future market demand for flexible pouches and rigid packaging will be shaped by multiple factors.
The continued growth of global e-commerce will create more opportunities for flexible pouches. Their lightweight, easy-to-transport, and space-saving characteristics align well with e-commerce logistics needs. Many food and daily necessity products sold online, such as snacks or condiments, increasingly use pouches for convenience and cost efficiency.
Rising consumer focus on health and sustainability will also influence packaging demand. For health, consumers prioritize freshness and safety, requiring packaging with superior barrier properties and hygiene standards. Both pouches and rigid packaging must improve materials and processes to meet these expectations. For sustainability, consumers prefer recyclable and biodegradable options, pushing businesses to invest in eco-friendly materials and drive the industry toward greener practices.
Industry trends will further shape demand. In the food and beverage sector, growing demand for convenient, ready-to-eat products will boost pouch usage, with portable juice or yogurt pouches gaining popularity. In premium alcohol and cosmetics, rigid packaging will remain dominant due to its ability to convey quality and prestige.
Economic development and regional differences will also play a role. In affluent regions, consumers demand high-quality, well-designed packaging, favoring rigid options for their added value. In less developed regions, price sensitivity may drive preference for cost-effective pouches.
7. Making Informed Packaging Choices
In the realm of packaging, flexible pouches and rigid packaging are like two distinct “contenders,” each showcasing unique strengths across materials, performance, cost, and environmental impact.
Flexible pouches shine with their significant cost efficiency, high space utilization, diverse design flexibility, strong environmental attributes, and versatile functionality. Their lightweight, foldable nature saves transportation and storage costs, while rich design options and eco-friendly properties appeal to consumers. However, limitations like limited protection, perceived lower quality, and constrained barrier performance make them less suitable for certain products.
Rigid packaging excels with its superior protection, ability to enhance product image, and ease of transportation and display, making it the go-to choice for premium or fragile products. Its durability provides reliable protection, and refined designs elevate brand prestige. Yet, higher costs, environmental drawbacks, and limited design flexibility restrict its versatility.
Thus, businesses must avoid one-size-fits-all approaches when selecting packaging. Product characteristics are the primary consideration, as different industries—food and beverage, personal care, pharmaceuticals—have unique physical and chemical requirements. Cost is another key factor, requiring a balance between initial procurement and long-term usage costs to ensure affordability. With rising environmental awareness, businesses should prioritize recyclable and biodegradables materials to minimize ecological impact.
Looking ahead, as packaging technology evolves and market demands shift, both flexible pouches and rigid packaging will face new opportunities and challenges. Businesses must stay attuned to industry trends, continuously explore innovative packaging solutions, and adapt to consumers’ diverse needs to thrive in a competitive market.